Slip, Chemical, and Stain Resistance
MMA can be tailored for varying slip resistance needs. By incorporating non-slip aggregates into the resin system, contractors can achieve textured, anti-slip finishes ideal for commercial kitchens, loading docks, or high foot-traffic areas requiring compliance with Australian Standard 4586-2013 for pedestrian surface materials.
The material’s resistance to chemicals, oils, fats, acids, alkalis and salts, makes it a go-to for environments prone to spillages. Unlike some coatings, MMA resists staining and discolouration over time—even under harsh cleaning regimens.
Waterproof
MMA resin systems can be delivered to be compliant with Australian Standard 4654.1-2012 for waterproofing membranes in external, above-ground applications, ensuring the asset is appropriately protected with the incorporation of a class 3 waterproof membrane within the system.
Easy Refurbishment
A seamless MMA floor only requires routine maintenance like many other resin flooring solutions. When the floor eventually reaches the end of its lifecycle, refurbishment is remarkably straightforward. New MMA layers chemically bond to the floor's existing MMA coating without the need for complete removal or any mechanical abrasion, creating a monolithic system without delamination risk. This allows for fast, cost-effective repairs with minimal surface prep—significantly reducing lifecycle costs compared to the full removal and replacement required for many epoxy or polyurethane systems.
The Challenges of MMA Flooring
Odours During Installation
One commonly cited challenge of MMA is the odour released during curing. While non-toxic and very low in VOC content, the smell can be noticeable and potentially disruptive in occupied spaces.
However, this challenge is manageable. Contractors can implement ventilation controls such as temporary extraction fans, negative air pressure setups, or performing installations outside of business hours to minimize impact. Once cured, the odour dissipates completely, leaving an inert, odourless surface.
Higher Initial Costs
MMA flooring can carry a higher upfront cost than standard epoxy or polyurethane coatings. However, this is often offset by its faster return to service, lower downtime costs, and longer lifecycle savings. In time-sensitive or critical environments, the operational savings from rapid turnaround often outweigh the initial investment.
Specialised Installation Required
Due to its rapid curing and chemical properties, MMA must be installed by trained, experienced applicators. Contractors unfamiliar with the material risk poor adhesion or curing issues. Selecting qualified installers is crucial for achieving MMA’s performance potential.
How Does MMA Compare to Other Resin Systems?
Compared to epoxy, polyurethane & polyaspartic flooring, MMA stands out in:
- Each coat of MMA cures in approx. 1 hour, allowing for full system installation within 1 day vs. 12-24 hours per coat of epoxy/polyurethane and full system installation from 2-5 days for comparable system thicknesses.
- MMA systems achieve full chemical cure within 2-3 hours from completion vs 7 days for typical epoxy/polyurethane systems.
- Temperature tolerance: MMA installs at temperatures as low as -30°C; epoxy, polyurethane and polyaspartic typically need temperatures above 10°C
- Substrate Relative Humidity: MMA resins can be installed to substrates with up to 92% RH vs 75% RH for epoxy, polyurethane and polyaspartic resins.
- Refurbishment: MMA’s ability to re-bond to itself simplifies future repairs without mechanical abrasion or the need to go back to the substrate.
- Odour: MMA has a stronger odour during cure compared to low-odour epoxy/polyurethane.
- While epoxy and polyurethane may be better suited to budget-sensitive projects or decorative finishes requiring high gloss, MMA excels where time constraints, hygiene, and performance under extreme conditions are priorities.
- MMA and polyaspartic resins have similar budgetary impacts on the project.
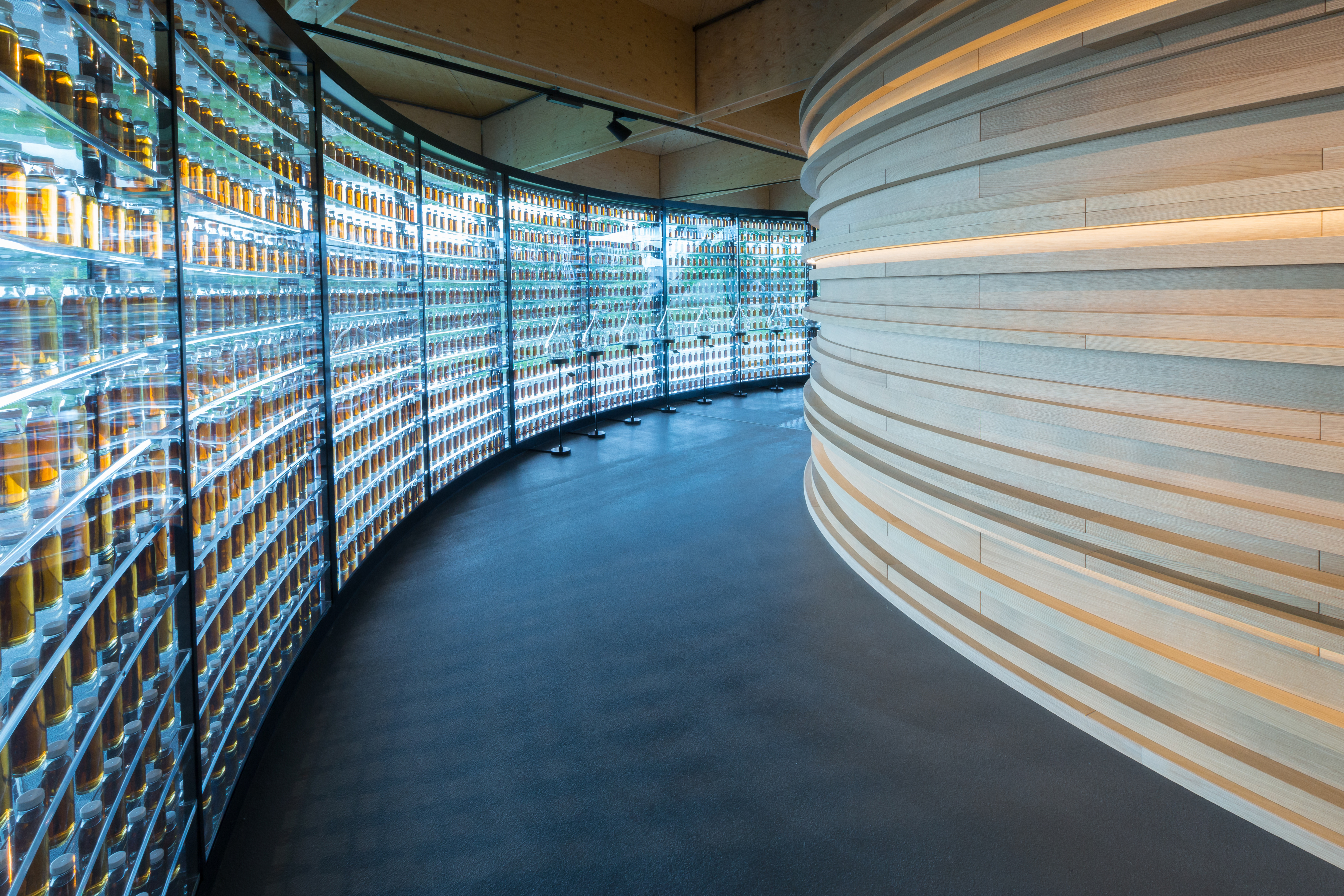